Benefits of DeMalong Hydraulic Filter Element
- High resistance to variable operating pressures and flowrates
- More pleats for hydraulic filter larger surface and filtration area
- Improved hydraulic system operation and reliability
- Reduced maintenance costs by consistent filtration efficiency
- Extended filter element life, low clean differential pressure
- Customized options with specific hydraulic filter element dimensions
- Technical consulting, engineering support and testing service
DeMalong Hydraulic Filter for long service life and reliable performance
DeMalong Hydraulic Filter Element also names hydraulic oil filter element, hyd filter element, which is used to maintain hydraulic system contaminants at low levels. These elements are available with various filter materials, different construction types and hydraulic filter micron ratings to ensure reliable filtration performance.
DeMalong Hydraulic Filter Element is an excellent and cost competitive filtration solution fit in hydraulic in line filters, hydraulic pressure filters, hydraulic suction filters, spin on hydraulic filter housing and return filters. DeMalong is glad to custom hydraulic filter elements with your own sizes and design.
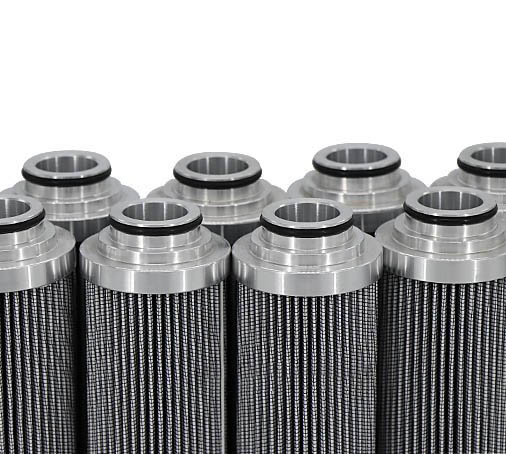
DeMalong hydraulic pressure filter element are ideal in medium and high pressure hydraulic filters to protect system parts like valves and hydraulic motors. Our pressure oil filter elements can withst...
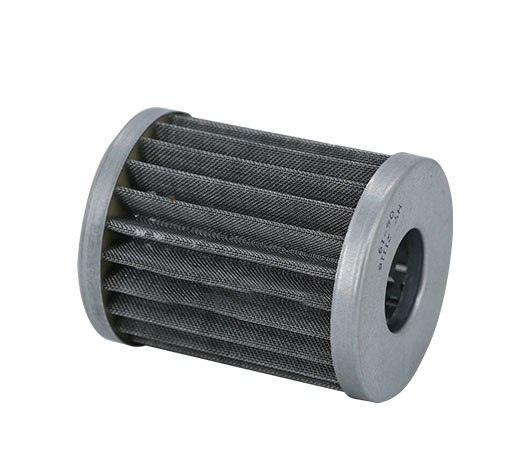
DeMalong suction filter elements specifically use to protect sensitive hydraulic pumps. It adopt stainless steel wire mesh material to remove particulate and decrease the cavitation risk with a minima...
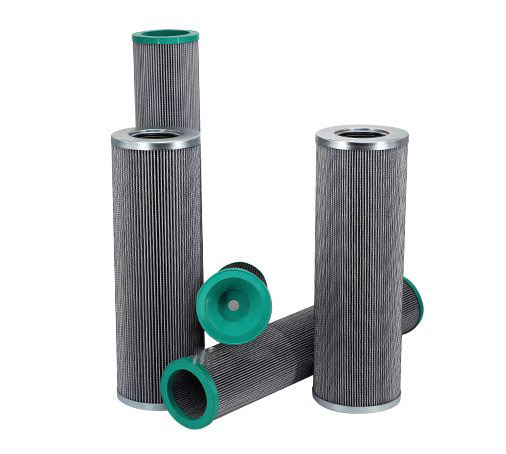
DeMalong In-line filter elements are used in low pressure in-line hydraulic filters. It has a large dirty holding capacity and longer lifespan with more pleats and surface area than most competitors. ...
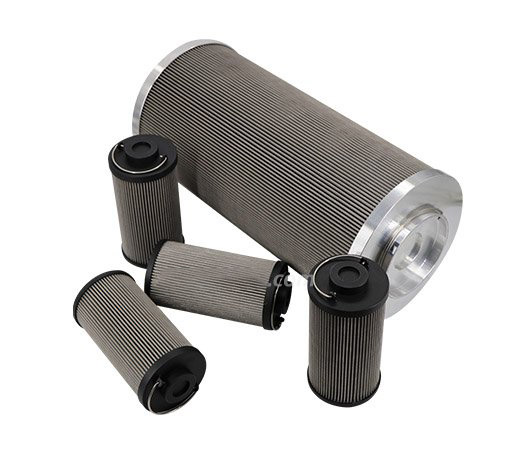
DeMalong return line filter elements are installed in hydraulic return filters to remove particle contamination from oil. Filter material of DeMalong return filter elements mainly includes glassfiber,...
- Detail Pics
- Drawing
- Process Technology
Send Inquiry Now
Frequently Asked Questions
If you have any questions, our FAQ section is a great place to get concise, accurate answers.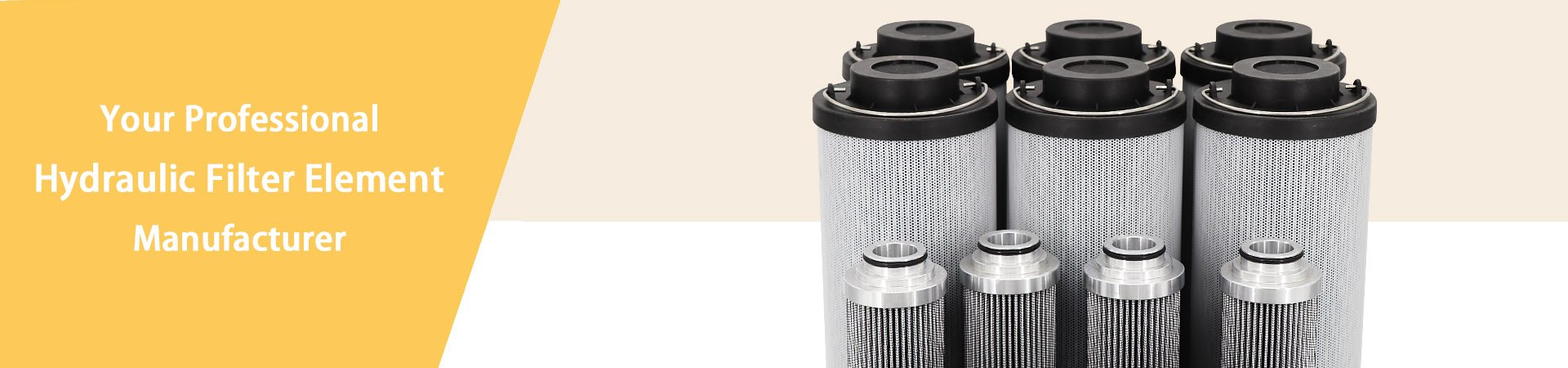
DeMalong Hydraulic Filter Element
Based on your oil cleanliness level requirements and hydraulic system applications, DeMalong offers glass fiber, stainless steel wire mesh, and paper filter materials. They are used as a surface or depth filtration to help you protect critical system components. The hydraulic filter micron rating is available from1 to 200 um with pressure up to 42 bar.
Compare with other hydraulic filters suppliers, DeMalong hydraulic oil filter element has a high dirt-holding capacity to ensure consistent filter efficiency and long element life. Meanwhile, our hydraulic filter price is more competitive. DeMalong always continues improving our hydraulic filter cartridge process technologies, quality standards, and cost control.
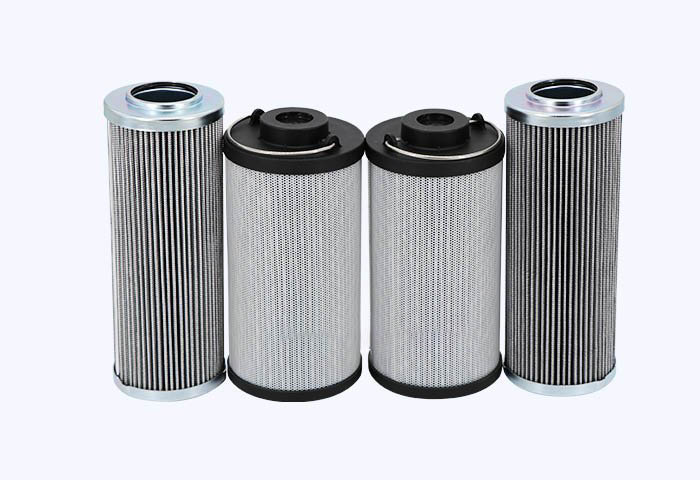
Having a comparable performance and same dimension, function, DeMalong hydraulic oil filter elements can be easily applied as many brands’ hydraulic filter replacement, such as Mahle hydraulic filter elements, Vickers hydraulic filter elements, Pall hydraulic oil filter elements, Hydac hydraulic filters, Parker hydraulic filter elements…
At present, DeMalong hydraulic filtration product line features more than 4,800 high-quality hydraulic filter elements. Whether hydraulic oil flows from outside to the inside, or from inside to outside, our engineers can help you design hydraulic filter cartridge with high strength, high removal efficiencies, and long service life.
If you want to keep the hydraulic system in low contamination, save maintenance cost and avoid expensive pump failures, oil changes, and unscheduled downtime, please contact us now.
No matter for standard or custom dimensions, DeMalong offers OEM for all hydraulic filtration solutions.
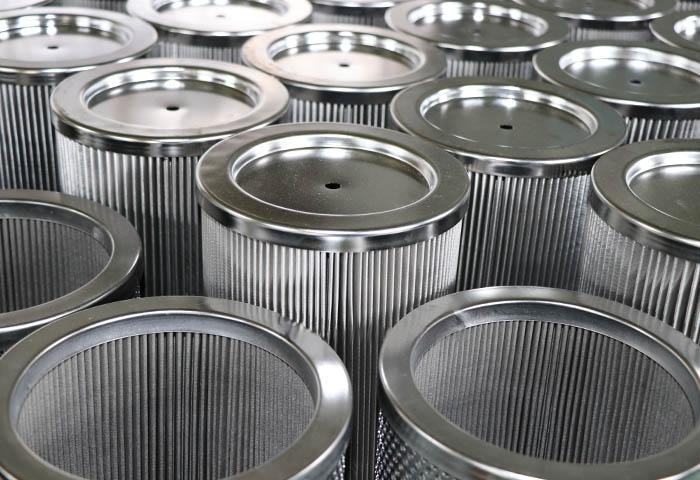
Hydraulic Oil Filter Specifications:
- Filter material: Glass fiber, paper, stainless steel wire mesh
- Filtration accuracy: 1μm ~ 200μm
- Working pressure: 10bar-420bar
- Working temperature: -30°C~+100°C
- Sealing material: nitrile, Viton, others on request
- End design: single or double open end, bypass valve with opening pressure options
Hydraulic Filter Element Application:
- Power generation
- Agriculture and construction
- Chemical processing
- Wind
- Oil and gas
- Compressors
- Power units
- Mobile hydraulics
- Factory equipment
- Coatings & Inks
Why choose hydraulic filter elements from DeMalong ?
- Direct Hydraulic Filter Element Manufacturer
DeMalong is a professional hydraulic filter elements manufacturer, so we have a better price and quality control ability on our hydraulic oil filter elements. The cost will be about half of your local supplier (including freight).
- 24 Hours Fully Support Service
Our support team will help you 24/7 with hydraulic filter system technical problems, we will one-to-one to check your installation dimension and details, so it is very easy to help you design or replace hydraulic filter elements. Free sample is available with quick delivery.
- Professional Production Technology&Staffs.
DeMalong has more than 18 years hydraulic elements production experience. Replacement and custom hydraulic filter oil cartridges are sold in 30+ countries.
- Strict Quality Control After-sale.
We ensure you that if there are any quality problems after-sale, we will reproduce for free. All DeMalong hydraulicfilter elements are integrated quality inspection before delivery.
How to change hydraulic filter elements?
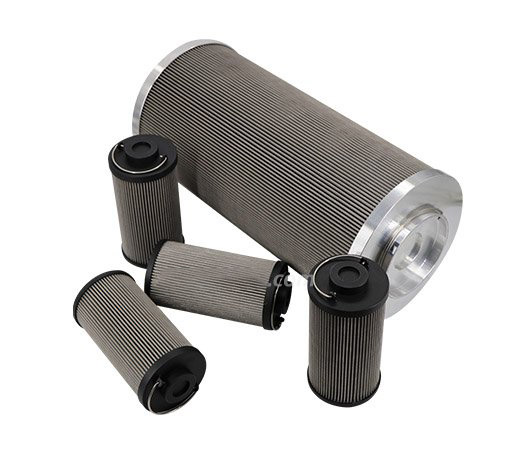
Usually when the filter is blocked with contaminants, reaching a setting drop of pressure. Hydraulic filter elements should be replaced immediately to ensure optimum and continuous filtration performance.
- Make sure the hydraulic system is off-line.
- Vent and drain the hydraulic filter housing.
- Take off the lid of the hydraulic oil filters and take out used hydraulic filter element.
- Set the new hydraulic filter element in place.
- Check and install the cover gasket to re-seal the hydraulic system.
Quality Assurance For DeMalong Hydraulic Filter Element
- Raw material procurement with certification
- Professional inspectors at every production process
- Advanced production and glue-injection equipment
- Strict testing before send-out based on ISO standards:
- Element collapse resistance as per ISO 2941
- Pressure drop versus flow characteristic as per ISO 3968
- Fatigue pressure testing as per ISO 3724
- Fluid compatibility as per ISO 2943
- Multi-pass filter ratings as per ISO 16889
What is your hydraulic filter element minimum order quantity?
We don’t have MOQ limited, usually with 1 PC.
What is your delivery time?
For hydraulic filter replacement, we have many brands in stock and ready to ship immediately.
For custom HYD filter elements, we will produce and deliver within 7-15 days.
What is your hydraulic filter element packaging and shipment?
Package: Carton or wooden case as your request.
Shipping:
- FedEx/DHL/UPS/TNT for samples or small order, directly to your company.
- By Sea from Qingdao or Shanghai port
- By air from Zhengzhou airport, 3-5 days arrival
How to get a quick quote of the hydraulic filter element?
Contact us at info@dmlfilter.com, and please tell us your present hydraulic filter housing structure or elements dimensions. Our support team will contact you as soon as possible.
What’re the terms of payment?
T/T 30-50% as deposit, and balance before delivery
Can I use my own logo on the hydraulic filter element?
Yes, we offer OEM service and customize brand logo or model numbers on the products are available.
Hydraulic Filter Element: Ultimate GAQ Guide
What is the function of a Hydraulic Filter Element?
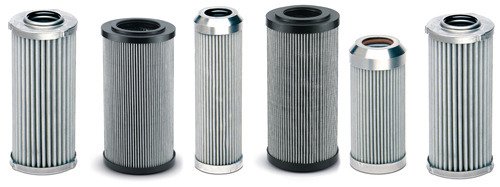
Hydraulic filter element
- Remove contaminants in hydraulic systems which is responsible for 80% of systems failure
- Reduce the cost of running hydraulic systems by preventing system downtime and frequent wear of components due to contamination
- Protect hydraulic systems components such as fittings, hoses, valves, pumps, etc. from contaminants that would otherwise cause damage
- Depending on the micron rating, hydraulic filters can remove very tiny contaminants (virtually invisible)
- Reduces frequency of systems maintenance and component replacement
- Ensures hydraulic system is safe and clean
What are Major Components of a Hydraulic Filter Element?
The major components of the hydraulic filter include:
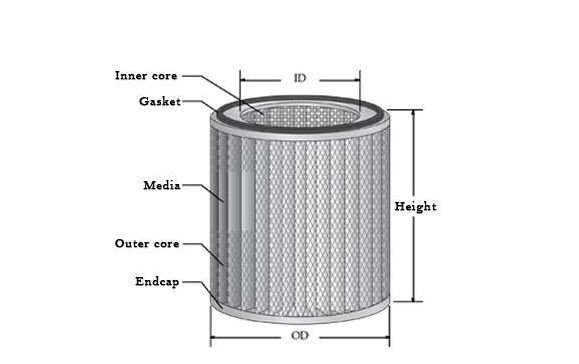
Parts of hydraulic filter element
· Center or Inner Tube Support
Most hydraulic applications have a large pressure differential across its elements.
Therefore, it has an inner tube support to increase the resistance of the hydraulic filtration elements to collapse.
· Wire Screens or Stainless Steel Wire Mesh
This is a multilayer or single structure that provides strength to the filter due to high flows.
· End Plate
These are zinc coated or stainless steel sheets in a variety of shapes to hold the tubular filters.
All hydraulic filter elements have two endplates, one at the top and the other at the bottom.
· Tubular Filter (Filtering Material)
This is the main filtering material with a number of pleats to increase the surface area and efficiency of filtration.
You can get a hydraulic filter with different tubular filters such as:
- Microglass on hydraulic filters
- Paper on hydraulic filters
- Stainless Steel wire mesh
· Adhesives
Most hydraulic filters have epoxy adhesives which bonds the inner cylinder, tubular filter, and end plates together.
· O-Ring Seals
The O-rings act as seals between the filter body and the upper end plates.
You will get an O-ring package according to the filter model.
· Notch Wire
This is a tightly coiled stainless steel wire that offers more support to the hydraulic filter element.
· Fin Tube
This is an aluminum alloy tube where the notched wire wraps around and forms a cylinder.
How Does a Hydraulic Filter Element Work?
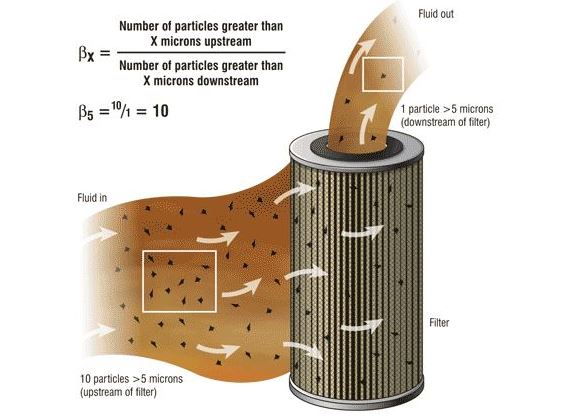
Working of hydraulic filter
The hydraulic filter elements work based on specific principles including:
1) Pressure Filtration
The filtration principle relates to filters that are in pressure lines and deliver the ultimate protection for fittings that are downstream.
You can use the pressure flow to your advantage by adding filters with ratings of around 2 micrometers or maybe less.
In the case of high flow velocities, you may experience a decrease in the effectiveness of the filters.
This will be as a result of disturbance to the particles within the filtration trap.
Pressure filtration is the most expensive mode of filtration due to high installation and maintenance cost.
The high cost comes as there is a need to purchase high-quality hydraulic filters to withstand the high pressure.
2) Return Filtration
The principle of the return line for filtration follows the following philosophy:
In case the reservoir, fluid, and anything that enters the reservoir have been filtered then it will continue to be clean.
Fortunately, you can depend on the return line that makes it possible to force fluid through finer filters.
The filters can be as fine as 10 micrometers to trap any form of contaminant in the fluid.
In this case, the fluid pressure is not very high and will not interfere with the design of the filter or housing.
It will, therefore, make it one of the most economical filtration processes.
3) Off-line Filtration
This is the process of filtering fluids in the hydraulic container in a totally different circuit.
It relieves the filters in the main flow of heavy filtration and increases system availability.
This will, in turn, lead to a decrease in the cost of operation.
Using filters off-line comes with its advantages and disadvantages.
The main disadvantage being that off-line filtration can have a high installation cost.
It involves a multi-pass filtration at controlled velocity flow that delivers greater efficiency.
4) Suction Filtration
Suction filtration is the process of separating solids from a solid, liquid mixture with an aim of retaining the solid.
It uses the principle of vacuum filtration to separate the solids from the solid-fluid mixture.
For instance, crystallization process depends on suction filtration to separate the crystals from the fluid.
A filter that is near the pump intake is in a very good position.
This is due to more efficiency as it does not have high pressure nor fluid velocity.
In case you add a restriction to the intake line, you will be able to offset the above advantages.
This may affect the pump life due to cavitation and mechanical damages by having a restriction at the pump inlet.
The fluid can be contaminated by cavitation and it may damage critical surfaces.
The destruction occurs from vacuum induced forces on the pump.
What Types of Hydraulic Filter Elements are Manufactured by DeMalong ?
The main types of hydraulic filter elements manufactured by DeMalong include:
- Microglass on hydraulic filters
- Paper on hydraulic filters
- Stainless Steel wire mesh
Here is a guide on filter replacement.
Which Filter Materials are used to Produce Hydraulic Filter Elements? Please Explain the Differences and Advantages of Each?
The main types of filter materials include:
· Microglass or Glass Fibers on Hydraulic Filters
This is a multilayer pleated structure that consists of synthetic Microglass fibers.
All the hydraulic filter elements consist of:
i. Epoxy adhesives to seal them from leaking
ii. Machining end caps to increase the integrity of the elements
iii. High resistance to collapse even at higher pressure.
iv. Wide range of micron rating with a deep filtration.
v. Combination of absorption layers that can remove both water and particles
The main advantages of using the Microglass elements include:
i. It has a higher dirt holding capacity in comparison with others.
ii. It allows for very few element change outs as it can last longer thus saving money and time.
· Paper on Hydraulic Filters
This is a single layer structure with pleat structures made of polyester fiber and paper.
The main features include:
i. High material strength and stability for flushing operations
ii. It is available in different micron ratings such as 5, 10, 20, and 40 micrometer micron ratings.
iii. The media packaging has full encapsulation in a sealant that eliminates the possibility of fluid bypass.
iv. It has a wider surface area that increases high flow performance and life of the filter element.
The main advantages of using the paper as hydraulic filter element include:
i. It saves cost as it is cheaper to acquire and maintain.
· Stainless Steel Wire Mesh
This is a single or multilayer pleated stainless steelwire mesh structure.
You can use it for surface filtration to protect the hydraulic pumps and remove particles from hydraulic fluid.
It is available in different micron ratings such as 25, 40, and 80 micrometer micron ratings.
You can also get custom micron ratings according to your specifications.
The main advantage of using the stainless steel wire mesh include:
i. It is easy to clean and maintain thus a longer service life.
ii. It is a cheaper alternative to glass fiber filter elements.
What are the Meanings of “Micron” and “Mesh” for Filtration?
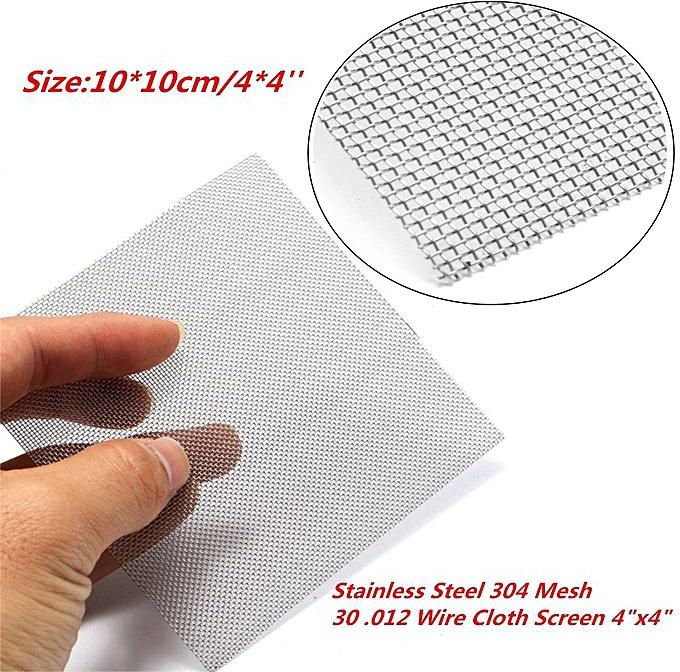
Micron and mesh
The units for measuring the size of the wire mesh are in terms of the number of mesh per inch.
Implying that, if there are 5 meshes, then within one inch there are 5 gaps.
The size of mesh openings differs according to the wire diameter of the wire mesh even for the same number of mesh.
A micron, on the other hand, is a measurement unit that represents a millionth of a meter.
It is also the ability of a fluid filter to remove the contaminants depending on the size of the particles.
So, the smaller the micron rating of a particular filter, the higher the efficiency of the filter.
What is a Filter Efficiency?
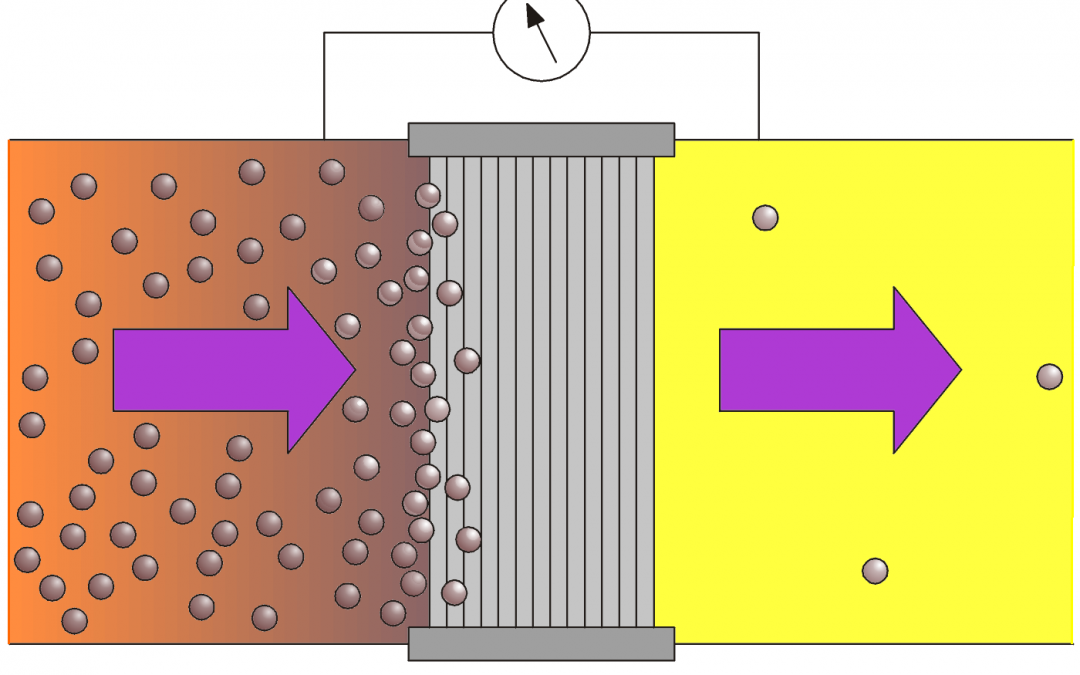
Hydraulic filter efficiency – Photo courtesy: Hydraulic solutions
Filter efficiency is the ability of a hydraulic filter to trap contaminants within the filter element.
It is a ratio of particles that a filter element cantrap over the number of particles in the upstream fluid.
You can be able to determine the efficiency of the hydraulic filter just by counting the number of downstream particles.
You can also tell filter efficiency depending on specific particle size ranges or the total number of particles of all sizes.
What is a beta rating?
Beta rating describes the efficiency of a filter in the retention by looking at the particles retained within the filter.
Larger beta rating is an indication of a good hydraulic filter with a more efficient particle retention rate.
Beta rating is often a subscript number for the micron size being considered.
For instance, β4μ means the beta rating for the filter at 4 microns.
It also denotes how efficiently 4 micron particles are removed by the hydraulic filter element.
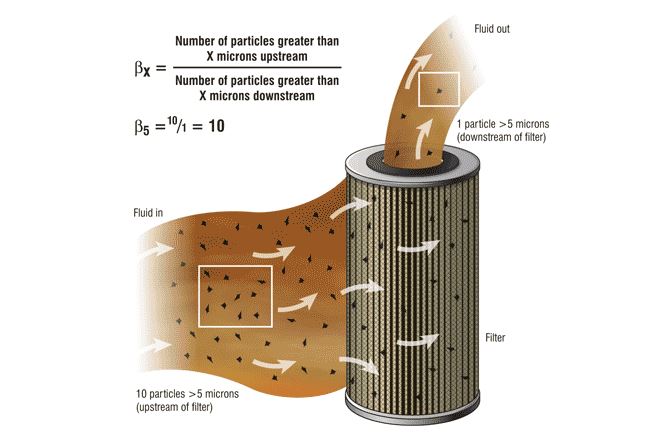
Beta rating – Photo courtesy: Machinery and Lubrication
What is the Difference between Absolute and Nominal Ratings?
A measure of the pore size in the filter media is expressed as either ‘Nominal’ or ‘Absolute’.
It also refers to the efficiency of the hydraulic filter element.
Nominal is a standard element of efficiency that depends on surface filtration.
Nominal rating is the percentage of particles of given sizes that hydraulic filters can capture.
For instance, 12 microns at 92% means the filter will remove 92% of particles of 12 microns in size.
Absolute rating, on the other hand, is a high element of efficiency that depends on a higher depth of filtration.
Absolute rating refers to the removal of all particles at a given micron size.
That is, 25-micron absolute means 100% of particles of size 25 microns or greater will be captured.
Absolute vs Nominal
These terms refer to the efficiency of the element.
Absolute is a high efficiency element that utilizes depth filtration (multi-layers).
Nominal is a standard efficiency element that utilizes surface filtration (single layer, i.e. wire mesh or paper).
ISO 16889: 1999 defines a depth filtration high efficiency (absolute) element as having a beta ratio of ssx>= 75, as determined by a multi-pass test.
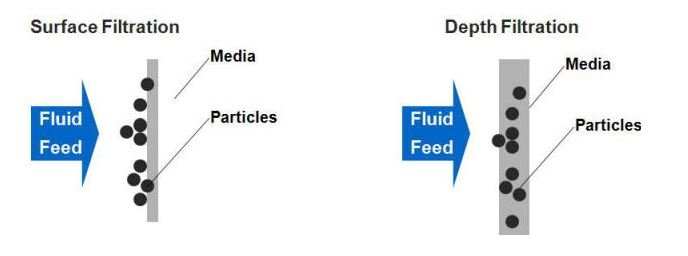
Filtration
No industry standard exists for determining the efficiency of a surface filtration standard (nominal) element, therefore it does not have a beta rating.
What is the Collapse Rating?
This is a type of rating that determines the ability of the filter to resist collapse.
You can rate the collapse rating through the differential pressure (PSID).
Differential pressure is the pressure difference from the inlet to the outlet of the filter.
Does more Pleats Number of Filter Paper mean Better Filtration?
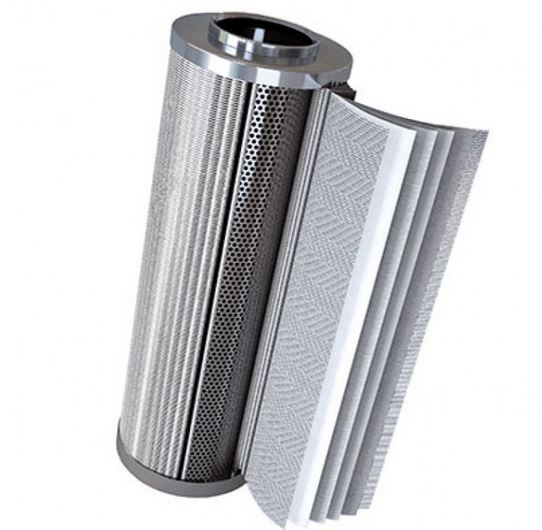
Pleated filter element
Yes, it is true that hydraulic filter element with more pleats number represents the ability to trap more contaminants.
This means that a hydraulic filter with a higher number of pleats of filter media is a better filter.
The fewer the pleats, the little the filtration media and thus a lower filtration capacity.
Having too many pleats can also lead to a lower flow rate and hence poor filtration efficiency.
What is the By-pass Valve or a Relief Valve?
A relief valve or a by-pass valve controls the flow of hydraulic fluid into the system.
The by-pass valve will open and allow the hydraulic fluid to flow into the system in case the filter chokes.
It helps in avoiding a situation where the hydraulic system would work without a hydraulic fluid.
In a situation where the filter pores are blocked completely with the contaminants, the system will trigger the by-pass valve.
It will open up and preset the pressure thus allowing unfiltered hydraulic fluid into the system.
What are the Design Temperatures of the Products?
The design temperatures for standard products are 90 degrees centigrade.
It is, however, possible to have different custom temperature specifications according to the filtration and model.
How to Calculate the P Across the Hydraulic Element?
You will need additional information to assist in the calculation of the P across the element.
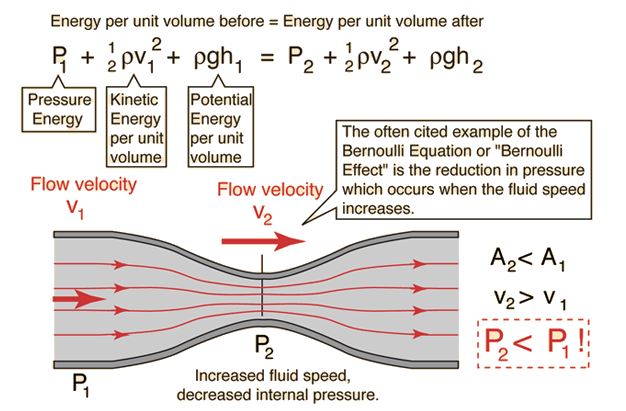
Bernoulli’s equation
The additional information will include:
i. The fluid viscosity at normal operating temperature
ii. The required filtration rating in um (microns)
iii. The type of element you are using in terms of collapse rating which can either be high or low collapse.
iv. The coefficient (K) factor from the conversion tables.
You can use the following formulae to calculate P across the element.
Other factors such as viscosity and specific gravity can change the P.
What does ISO Code Mean?
You can measure oil cleanliness in terms of ISO code 4406.
Each level in the ISO code is a representation of the number of particles within a milliliter of oil.
This can be equal to or larger than 4, 6, or 14 microns in diameter.
All the counts are cumulative because for instance a particle that is larger than 6μ is also larger than 4μ.
Each ISO code represents a particular range of particle counts.
The threshold of the particle count for each ISO code is double that of the one before.
For example, ISO code 19/17/14 means that:
- Particles of diameter greater than or equal to 4μ have ISO code 19.
- Diameter that is greater than or equal to 6μ have ISO code 17.
- Diameter that is greater than or equal to 14μ have ISO code 14.
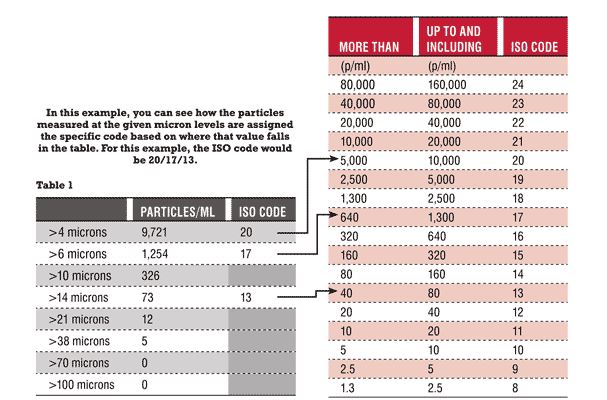
ISO Code – Photo courtesy: Machinery and Lubrication
Should I Filter New Hydraulic Oil or “Looks Clean” Oil?
Yes, you should filter new hydraulic oil.
This is because new oil might contain particles in the wear range that exceeds the maximum contamination levels.
The manufacturer may specify a particular contamination level but you can never be sure about such specifications.
Apart from that, you can only see particles larger than 40μm with your naked eyes.
There are millions of small particles that you may not see that contaminates the oil.
The smaller particles slowly cause wear and tear of the machine components thus introducing more contaminants.
This can lead to damages on the machine and more downtime during system failures and repair.
Furthermore, the contaminated oil reduces hydraulic efficiency during normal hydraulic operations.
It is, therefore, important to clean the oil to as low as ISO class 13/11/8 through by-pass filtration or any other form of filtration.
This will not only prolong oil life, and reduce downtime, but also increase the efficiency of the oil.
What is the Benefit of Achieving ISO class 13/11/8, Over New Oil on 19/17/14?
The minimum requirement for cleaning new oil is ISO level of 19/17/14.
At this particular level, oil particles are pumped around at full flow throughout the hydraulic system at all times.
For instance, a hydraulic system with a 100L/min flow, that operates for 24 hours a day throughout the year.
It will be capable of pushing up to 592.1kg of dirt through the pumps and machine components.
This increases the risk of damage to the machine components as the contaminants are in excess.
In case you clean and maintain the same system at ISO 13/11/8 the pumps and machine components would see fewer contaminants.
A reduction of the cleanliness of the oil to level 13/11/8 will signify a contaminant reduction to 9.5 kg.
This a reduction in weight of contaminants by 98.4% of the oil at ISO 19/17/14.
This reduces the chances of damage on the pumps and machine components.
You will be able to run the machine with minimal downtime and at lower cost of maintenance.
This reduction in contamination seen by the hydraulic components prolongs their lives.
How to Measure Oil ISO Cleanliness?
To measure the ISO code cleanliness of any oil, you can use an off-line or inline particle counter.
Apart from that, you can also use the automatic particle counter (APC).
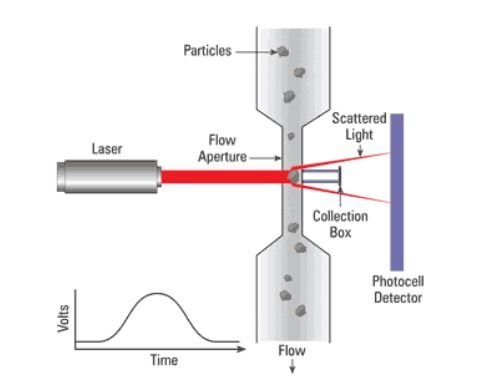
Particulate counter for contamination control – Photo courtesy: Machinery and Lubrication
At the moment, the calibration standard for the automatic particle counter is at ISO 11171.
First, you will set the particle counter according to the right working specifications usually by a factory calibration.
You will also prepare samples of the oil that you need to test.
After that, you will pass a known volume of oil through the flow aperture of the device.
As that continues you will shine a laser beam from one side to the other side of the aperture.
Additionally, you may also consider using the pore blockage technique to measure oil ISO cleanliness.
You can, therefore calculate the particle size by:
Checking voltage drop through shadow formation from particles on the opposite side of the tube via light scattering techniques.
The result will be different particle counts depending on the oil sample that you will be measuring.
This will be a representation of various micron levels that will indicate the cleanliness of the oil.
You will then refer to the ISO 44046:99 as the standard for fluid cleanliness.
You will assign a code number according to the particle count value at three different micron levels.
This includes:
- Greater than 4 microns which means the oil contains more than 5000 particles per milliliter of the oil.
- Greater than 6 microns which implies that the oil contains more than 640 particles per milliliter.
- Greater than 14 microns which means the oil contains more than 40 particles per milliliter.
What is the ISO 16889 Multi-pass Test?
The ISO 16889 multi-pass test is a particular lab-based procedure and standard for testing dirt holding capacity.
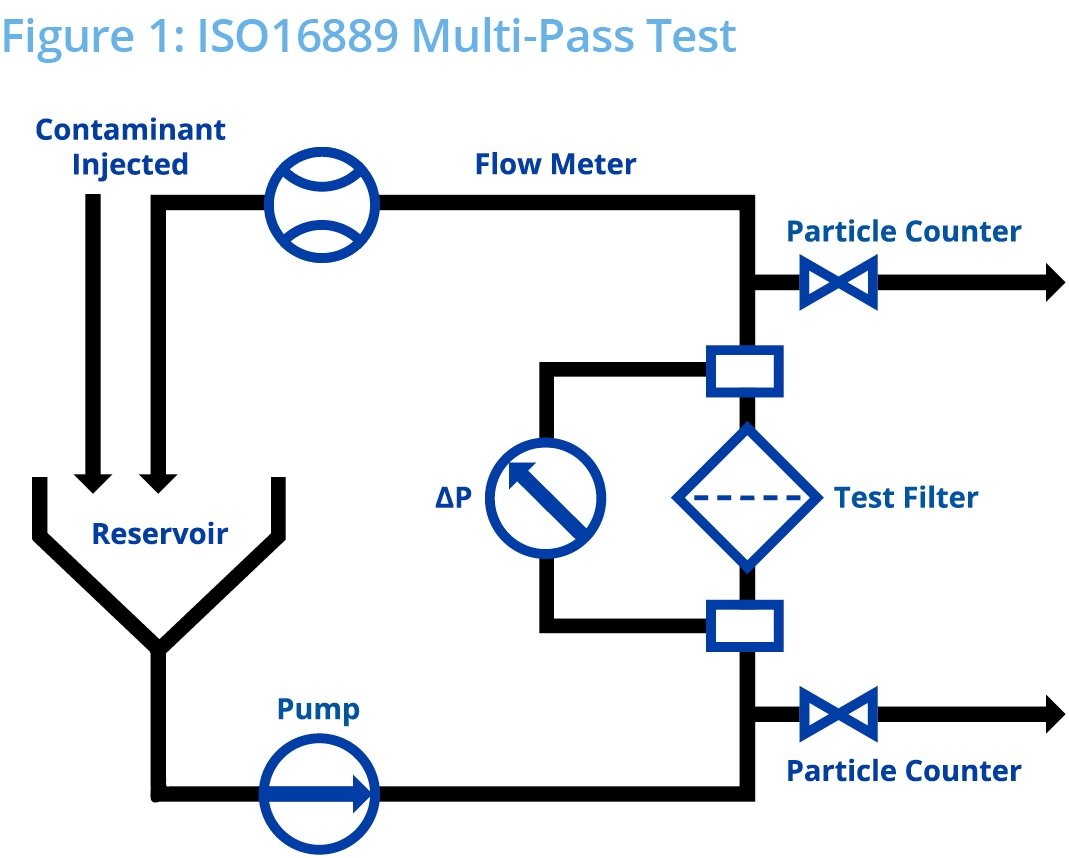
Multi-pass test – Photo courtesy: Hypro filtration
The procedure has to have reproducible test data that you can use to evaluate the particle removal efficiency (Beta Ratio).
It measures the particle removal capacity of the hydraulic filter element in relation to dirt particle ingression.
This will result in an increase in the differential pressure over the element life of the hydraulic filter element.
Is Hydraulic Element Cleanable?
Yes, hydraulic elements are cleanable.
You can only clean the wire mesh element and glass fiber element.
Paper elements are not cleanable and you will replace them as soon as they are blocked.
How to Clean, Cleanable Elements? How many Times Can You Clean Them?
You can clean the cleanable elements including wire mesh and metal fiber elements up to a maximum of 5 times.
Cleaning Wire Mesh Elements
You can clean the wire mesh element using different cleaning methods under the following procedure.
Step One: Soaking the Wire Mesh Hydraulic Filter
First, you need to remove the wire mesh element from the hydraulic machine.
The most common way of cleaning the wire mesh element is by washing it in a clean solvent.
Apart from the clean solvent, you can also use hot soapy water ammonia solution.
You will then deep and soak the hydraulic filter element in the solvent or solution to soften the contaminants.
Step Two: Brushing off the Contaminants
Using a soft bristle brush, remove the contaminants that might stick to the wire mesh element.
Brush them off gently for a while and ensure that you leave nothing on the wire mesh elements.
Do not use a wire brush or any form of abrasive material that would damage the wire mesh element.
Step Three: Rinsing the Element
After that you will rinse the wire mesh element with clean water.
You can either soak it in clean water or use a hose pipe to splash clean water on the element.
Step Four: Drying the Element
You can air the wire mesh element to allow it to dry.
You can as well blow off the wire mesh element using clean air to get rid of the water.
Alternatively, you can use the more expensive ultrasonic cleaning method.
In this case, you will place the wire mesh filter element in the ultrasonic device for a while.
After that, you will remove the wire mesh element and replace it for reuse.
This method also applies to the metal fiber elements.
Despite the cost, it is more convenient and will save you a lot of time and energy.
Remember, you can also go for self-cleaning filters.
How Long is the Service Life of Hydraulic Filter Element?
The service life of hydraulic filter elements will depend on different variables.
Some of the factors that you need to know in order to calculate the length o service life include:
i. The dirt content or cleanliness level of the hydraulic filter element
ii. The dirt ingression rate of the hydraulic system
iii. The dust holding capacity of the filter element
The higher the quality of the hydraulic filter element, the higher the dirt holding capacity.
This implies that it would hold more dirt for a longer period and it would last longer.
Whenever the filter element blocks, you can either clean it or replace it.
On average, you should be able to replace the filter elements after a period of 6 months for better efficiency.
Should I Replace Hydraulic Filter Element Regularly?
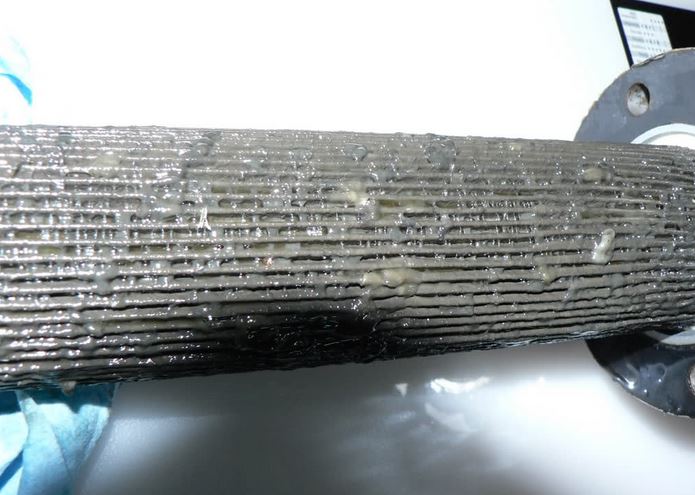
Dirty hydraulic filter element
You might be changing the hydraulic filters too late or too early if you change your filter elements on schedule.
You will be wasting a lot of money on the hydraulic filter elements if you change them early.
This means that you will be changing them before all their dirt-holding capacity is used up.
In case you change them late, especially after the filter has gone on bypass, you risk the following:
i. There will be an increase in particles in the oil.
ii. More particles in the system pose a great danger to the machine components.
iii. It will quietly reduce the service life of every component in the hydraulic system.
iv. In the long run, it will cost you more to make repairs and replacements.
You should, therefore, change your filters when all their dirt-holding capacity is used up, but before the bypass valve opens.
You will need a mechanism to monitor the pressure drop or restriction to flow across the filter element.
The mechanism will alert you when the hydraulic filter element reaches that point.
The best solution, however, is the continuous monitoring of pressure drop across the filter.
How to Change Hydraulic Filter Elements?
You need to replace the hydraulic filter element when filter reaches setting drop of pressure or blocked with contaminants.
To ensure continuous and optimum filtration performance you need to replace the hydraulic filters through the following procedure:
Step One: Switching the Hydraulic Machine Off-line
First, you have to make sure the hydraulic system is off-line.
You will be reducing the chances of injury and creating an ample working environment.
Allow the system to cool off for a while before engaging in the replacement procedure.
Step Two: Venting and Draining the Hydraulic Filter Housing
At this stage, you will remove the hydraulic filter housing to expose the hydraulic filter.
After that, you will drain all the hydraulic fluid from the system to avoid unnecessary spillage.
Step Three: Replacing the Hydraulic Filters
Remove the lid of the hydraulic oil filters and take out used hydraulic filter element.
Set the new hydraulic filter element in place.
Check and install the cover gasket to re-seal the hydraulic system.
Take the hydraulic system back on-line and let the filtration process continue.
Can a Hydraulic Filter Element Remove Moisture From Oil?
Yes, hydraulic filter elements can remove moisture from oil but that will depend on the type of hydraulic filter.
Even though hydraulic filters are good, they cannot be perfect in every sense.
For instance, hydraulic filters won’t stop water from getting into the system.
In case water gets into the system, it can cause all manner of issues.
However, you can equip your system with the best hydraulic filters that can remove moisture from oil.
This will result in less maintenance and an increased lifespan for your machinery.
You can use hydraulic filters such as cellulose depth filters to remove dissolved and free water contamination from oil.
As oil passes through the cellulose filter, the long cellulose fibers absorb moisture within the filter media, leaving the oil dry.
What Type of Oils Can go through a Hydraulic Filter Element?
Hydraulic filter elements can filter different types of oils.
The micron rating of the hydraulic filter will determine the speed at which the oil flows through the hydraulic filter.
The Element is Newly Changed but Indicator Activates Immediately. Why?
You might replace a blocked hydraulic filter element with a new one but the pressure indicator is still active.
The indicator is a mechanism that detects pressure throughout the element.
This means that the pressure system within the hydraulic system is experiencing some difficulties for some reason.
This can be as a result of the following:
i. The new element is clogged
You may replace the hydraulic filter with a clogged element.
You might not be able to detect the clogging from the surface view of the 3C, 8C fine elements.
Also, when replacing the used oil is replaced with new oil, dust mixing occurs through the oil refill method.
This may cause the element to clog thus activating the indicator immediately.
ii. High oil viscosity
High viscosity and low ambient temperature may activate the indicator.
In this case, if you proceed with the operation continues for a while, the indicator will restore.
iii. Wrong Element Replacement
You might replace the hydraulic filter element with the wrong type of filter element.
When you install an element whose filtration is finer that the previous model, the element may clog.
Why Filter Leaked Soon After the Hydraulic Element was Installed?
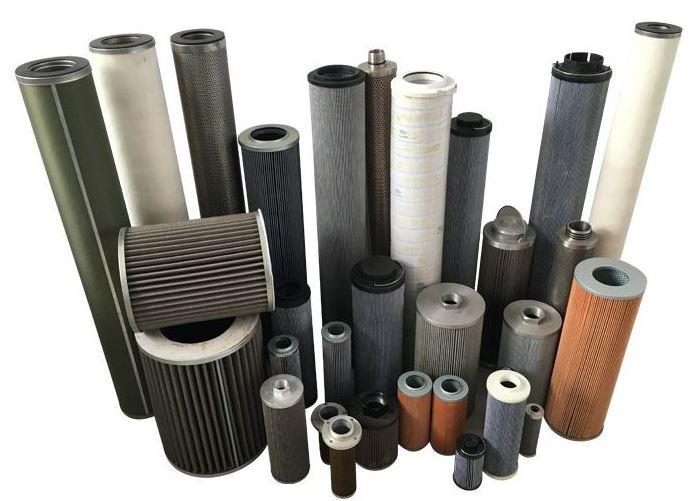
Different types of hydraulic filters
You may experience leakages as soon as you replace or install a new hydraulic filter element.
To avoid the leakage, make sure that you consider the following:
i. You need to make sure that you install the correct hydraulic filter element following the right instructions to the letter.
ii. You should also ensure that you remove the old sealing gasket from the engine mounting base plate.
Be careful not to warp or damage the base plate.
i. Make sure that the filter fits correctly after cleaning the surface of the engine.
ii. You have to confirm that the filter is correctly fitted with the sealing gasket provided with the filter.
This comes after applying oil on the surface of the gasket.
i. Evaluate the threaded stud and ensure it isn’t loose or damaged.
ii. Ensure that you properly tighten the filter as over or under tightening of the filter may lead to leakage.
How to Choose Most Appropriate Hydraulic Filter Element for your System?
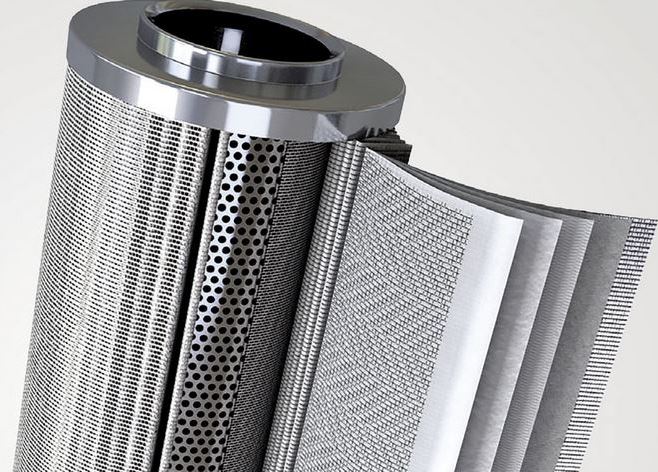
Hydraulic element structure
You need to understand your hydraulic system before deciding on the appropriate hydraulic filter element.
Apart from that, you need to look at the following:
i. Type of Hydraulic Filter
There are two main types of hydraulic oil filter which are surface and depth filters.
The surface filter will remove contamination from the surface of the oil.
It is useful in applications where gravity feeds the oil through space.
A depth filter, on the other hand, involves submerging the hydraulic filter in a reservoir or chamber.
It will remove particles from the entirety of the body of fluid.
Depth filters, therefore, are more effective and retains a larger amount of contamination and unwanted particles before cleaning or replacement.
ii. The Material of the Hydraulic Filter
The type of materials use to make hydraulic filters will vary according to the cost.
Glass fiber filters are more expensive but they are more efficient especially in a depth filter.
Glass is also non-reactive, implying that you can use it with any type of hydraulic fluid.
Metal filters are also reasonably efficient, but they cannot be used with all types of hydraulic fluid.
This is because some of the hydraulic fluids are incompatible with some metals.
You can also use the magnetic filter system where it is appropriate to use a metal filters.
It works as a depth filter and uses a magnetic charge to attract metal particles that may have entered the fluid system.
Cellulose or paper also make good hydraulic fluid filters, but has a short life span thus frequent replacements.
Even though they are cheaper than the other types, they could end up costing more in the long run.
This is because of potential damages and regular downtime for replacements if they are not replaced often enough.
Generally, glass fiber is the best choice despite high cost it does the best job and will not need frequent replacements.
The disadvantage of a glass fiber filter is actually on its strength.
The high filtering ability can lead to undesirable pressure drop in the system.
iii. Pressure Drop in the System
It is important to check how a drop in hydraulic system pressure will affect performance and productivity.
This is especially significant if you are considering switching to glass filters from another material type.
Consider also whether the drop in pressure leads to unnecessary adjustments of pressure relief valves, causing dangerous pressure buildup elsewhere.
The options of hydraulic oil filters do not end after material type and construction, as there is still the issue of ratings and specifications to contend with.
iv. Hydraulic Filter Ratings
All hydraulic filters have an ISO 4406 rating.
The lower the code of any hydraulic filter, the better it is at contamination removal.
You should also consider the beta ratio of the hydraulic filters.
This is the ratio of particles found upstream of the filter divided by the number of particles found downstream.
The higher the beta ratio, the better the hydraulic filter element, and thus the effectiveness.
v. Flow Rate of the Hydraulic Filter
You have to confirm that the flow rate of the filter is compatible with the flow rate of the machinery.
In case the flow rate is too fast, the filter will not be able to remove the contaminants effectively.
In case it is too slow, the hydraulic filter element could become clogged quickly.
vi. Operation Pressure of the Hydraulic System
You should look at the operational pressure of the hydraulic system as the filter must withstand that force.
vii. Port Size of the Hydraulic Filter
You need to make sure that you can connect the filter to the equipment or machine.
You should look at the port size of the filter and ensure it is compatible with the machinery.
There is a lot to consider, but choosing the most suitable hydraulic filter is an exercise worth spending time on.
This is because it can determine the performance and lifespan of your hydraulic equipment.
It will also save on downtime and replacement costs in the long run
Why DeMalong Hydraulic Filter Elements are of Good Quality?
You should consider purchasing your filter elements from DeMalong because of the following reasons.
- The process of raw material procurement goes hand in hand certification
- DeMalong employs professional inspectors at every production process
- It has advanced production and glue-injection equipment
- It adheres to strict testing before send-out based on ISO standards.
The main ISO Standards it adheres to include:
i. Element collapse resistance as per ISO 2941
ii. Pressure drop versus flow characteristic as per ISO 3968
iii. Fatigue pressure testing as per ISO 3724
iv. Fluid compatibility as per ISO 2943
If I Fit a Good Quality Hydraulic Filter, Can I Use Low Quality Oil?
Having a quality filter will not save your hydraulic system from damage if you use poor or low quality oil.
Low quality oil generally means the oil additives deteriorate quicker, putting more stress on the engine.
Make sure you use good quality oil and hydraulic filter elements.
Can I Use My own Logo on Hydraulic Filter Element?
Yes, DeMalong offers OEM service and customize brand logo or model numbers on the products.
Can I Customize Hydraulic Filter Element when Ordering from DeMalong ?
Yes, our support team will help you 24/7 with hydraulic filter system technical problems.
DeMalong will check your installation details and dimensions, making it easy to assist you design custom hydraulic filter elements.
We can also assist you with special applications, like magnetic oil filter element or anti-static filter elements.
What is the Sample Policy for DeMalong ?
DeMalong offers free samples with quick delivery.
You can contact us directly to discuss more information.
Does DeMalong have Hydraulic Filter Element Cross Reference?
Yes, DeMalong has hydraulic filter element cross reference services.
You can send us the model number, such as Hydac 1300r010bn4hc and we will send you our detailed quote immediately.
The replacement hydraulic filter element from DeMalong mainly includes Mahle, Parker, Bosch, Eaton, Pall, Hydac, Boll, and Norman among others.
What is your Hydraulic Filter Element Minimum Order Quantity?
DeMalong have no MOQ request, call us about your replacement or custom filter element needs.
What is Your Delivery Time?
The delivery time will vary according to the types of hydraulic filter element you desire.
For hydraulic filter replacement, we have many brands in stock and ready to ship immediately.
For custom HYD filter elements, we will produce and delivery within 7-15 days.
How to get a Quick Quote of DeMalong Hydraulic Filter Element?
Contact us at info@dmlfilter.com and please tell us your present hydraulic filter housing structure, or elements dimensions.
Our support team will contact you as soon as possible.
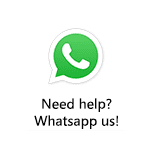